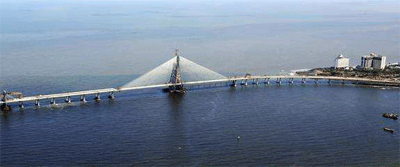
A triumph of precision engineering
Introduction The Bandra-Worli Sea Link (BWSL) is a civil engineering marvel spanning an arc of the Mumbai coastline. With its cable-stayed towers soaring gracefully skywards, the sea link is a reflection of the modern infrastructure that Mumbai is adding in its progress towards becoming a world-class city.
The BWSL project is a part of the Western Freeway Sea Project, which, in turn, is a part of a larger proposal to upgrade the road transportation network of greater Mumbai. In the first phase it will connect Bandra to Worli whereas in the subsequent phases the plans are to take it further to Haji Ali and then to Nariman Point. It is a connecting bridge linking the city of Mumbai with its western suburbs and has the potential to bring about permanent and far reaching changes in the travel patterns of the area. The Bandra-Worli Sea Link is primarily meant to provide an alternative to the Mahim Causeway route that is presently the only connection between South Mumbai and the Western and Central suburbs. The project starts from the interchange at Mahim intersection, i.e. intersection of Western Express Highway and Swami Vivekanand Road at the Bandra end, and connects it to Khan Abdul Gaffar Khan Road at the Worli end. The project has been commissioned to offer a quicker alternative to the north-south traffic that presently amounts to approximately 125,000 cars a day. The project has been commissioned by the Maharashtra State Road Development Corporation Ltd (MSRDC) and the Maharashtra Government and is being built by HCC (Hindustan Construction Company). As a builder of landmark infrastructure projects around the country, HCC has handled numerous challenges both in terms of location and technology. The BWSL project offered HCC an opportunity to accomplish one more feat: to construct an eight-lane freeway over the open sea for the first time in India. Highlights in brief • India’s first bridge to be constructed in open-sea conditions
• 4.7 km, twin, 4-lane independent carriageway bridge across the open sea
• 16-lane toll plaza with 20-m wide promenade together with state-of-the-art traffic monitoring, surveillance, information and control systems
• 2342 pre-cast segments for total bridge with varied width
• 40,000 MT of reinforcement, 23,0000 cum of concrete, 5,400 MT of Post tensioning strands and bars used
• Osterberg cell technology used for the first time in India to check pile strength (for up to 9600 MT).
• Engagement of Asian Hercules, one of the largest floating shear leg crane in the world for shifting 1,260 MT launching truss from Bandra end to Worli end of the main cable stay bridge
• Largest span for cable-stayed bridge in India
• Up to 25-m high pier in open sea, giving ample headroom to marine traffic
• Use of Polytron Disc in bearings on piers for the first time in India
Project overview
The entire project was originally conceived as one large project comprising, different components, but in order to accelerate the overall construction schedule, the project has been divided into five construction packages :- Package I: Construction of flyover over Love Grove junction at Worli Package II: Construction of cloverleaf interchange at Mahim intersection Package III: Construction of solid approach road from the Mahim intersection up to the
start of the Toll Plaza on the Bandra side and a public promenade Package IV: Construction of Cable-Stayed Bridges together with viaduct approaches
extending from Worli up to the Toll Plaza at Bandra end, Intelligent Bridge
System (IBS). Package V: Improvement to Khan Abdul Gaffar Khan Road Package IV is the largest and main phase of Bandra-Worli Sea Link Project.
Main features of this technically challenging package are:
• Cable-Stayed Bridge including viaduct approaches extending from Worli up to Toll Plaza at Bandra end
• Modern Toll Plaza The work under this package was awarded to HCC. Details of Package – IV Main Bridge structure The bridge consists of twin continuous concrete box girder bridge sections for traffic in each direction. Each bridge section, except at the cable-stayed portion, is supported on piers typically spaced at 50 meters. Each section is meant for four lanes of traffic, complete with concrete barriers and service side-walks on one side. The bridge alignment is defined with vertical and horizontal curves. The bridge layout is categorized into three different parts:
• Part 1 – The north-end approach structure with Pre-Cast (PC) segmental construction.
• Part 2 – The Cable-Stayed Bridge at Bandra channel is with 50m -250m-250m-50m span arrangement and the Cable-Stayed Bridge at Worli channel is with 50m-50m- 150m-50m-50m span arrangement.
• Part 3 – The south end approach structure with Pre-Cast segmental construction.
Part – I North End approach structure The bridge is arranged in units of typically six continuous spans of 50 meters each.
Expansion joints are provided at each end of the units. The superstructure and substructure are designed in accordance with IRC codes. Specifications conform to the IRC standard with supplementary specifications covering special items. The foundation consists of 1.5 meters diameter drilled piles (4 nos. for each pier) with pile caps. Bridge bearings are of Disc Type.
The bridge has been built utilising the concept of Pre-Cast, post-tensioned, segmental concrete box girder sections. An overhead gantry crane with self-launching capability is custom built by the company to lay the superstructure of the precast segments. The Pre-Cast segments are joined together using high strength epoxy glue with nominal prestressing initially. The end segments adjacent to the pier are short segments “cast-in-situ joints”. Geometrical adjustments of the span are made before primary continuous tendons are stressed.
Segment types are further defined by the changes in the web thickness and type of diaphragms cast in cell. The segment weights vary from 110 tons to 140 tons per segment. The segment length varies from 3000 mm to 3200 mm. Deck post tensioning is performed at the completion of the erection of each 50m bridge span. Part- II Cable-Stayed Bridge The cable-stayed portion of the Bandra channel is 600 meters in overall length between expansion joints and consists of two 250-meter cable supported main spans flanked by 50 meters conventional approach spans. A centre tower, with an overall height of 128 meters
above pile cap level, supports the superstructure by means of four planes of cable stay in a semi-harp arrangement. Cable spacing is 6.0 meters along the bridge deck.
The cable-stayed portion of the Worli channel is 350 meters in overall length between expansion joints and consists of one 150 meters cable supported main span flanked by two 50 meters conventional approach spans. A centre tower, with an overall height of 55 meters, supports the superstructure above the pile cap level by means of four planes of cable stay in a semi-harp arrangement. Cable spacing here is also 6.0 meters along the bridge deck.
The superstructure comprises twin precast concrete box girders with a fish belly cross sectional shape, identical to the approaches. A typical Pre-Cast segment length is 3.0 meters with the heaviest superstructure segment approaching 140 tons. Balanced cantilever construction is used for erecting the cable supported superstructure as compared to span-byspan construction for the approaches. For every second segment, cable anchorages are provided.
A total of 264 cable stays are used at Bandra channel with cable lengths varying from approximately 85 meters minimum to nearly 250 meters maximum. The tower is cast in-situ reinforced concrete using the climbing form method of construction. The overall tower configuration is an inverted “Y” shape with the inclined legs oriented along the axis of the bridge. Tower cable anchorage recesses are achieved by use of formed pockets and transverse and longitudinal bar post-tensioning is provided in the tower head to resist local cable forces.
A total of 160 cable stays are used at Worli channel with cable lengths varying from approximately 30 meters minimum to nearly 80 meters maximum. Like the Bandra channel, the tower here is also cast in-situ reinforced concrete using the climbing form method of construction but the overall tower configuration is “I” shape with the inclined legs. Similarly, tower cable anchorage recesses are achieved by use of formed pockets.
The foundations for the main tower comprise 2 meter-drilled shafts of 25 meters length each.
Cofferdam and tremie seal construction have been used to construct the six-meter deep foundation in the dry. Part – III South End approach structure This portion of the bridge is similar to the North end approach structure in construction methodology with span by span match cast concrete box girder sections. Toll Plaza A modern toll plaza with 16 lanes is provided at the Bandra end. The toll plaza is equipped with a state-of-the-art toll collection system. A structure is provided at this location to house the control system for the ITS. Intelligent Bridge System The toll station (TP) and collection system will provide for three different types of toll collection, as follows:
– Fully automatic system: Electronic payment through On board Units mounted on the vehicles which allow passage without stopping.
– Semi-automatic system: Electronic payment through a smart card, which allows payment without having to pay cash.
– Manual toll collection: Payment of toll by cash, requiring vehicle drivers to make cash payment to a toll attendant, and stopping for cash exchange.
The intelligent bridge system will provide additional traffic information, surveillance, monitoring and control systems. It comprises CCTVs, traffic counting and vehicle classification system, variable message signs, remote weather information system and emergency telephones. The control centre located near the toll plaza is housed with the
electronic tolling controls. The transmission system comprises fiber-optic cable housed in PVC conduits running parallel to the Bandra-Worli corridor. In addition, facilities to assist enforcement are provided in the form of pullout locations, which will allow drivers and enforcement officers to safely pullout of traffic. Power Supply Distribution and Road Lighting System A reliable and dependable power supply has been arranged for the entire project. It will also house diesel generator sets and auto mains failure panels to cater to critical load, e.g., monitoring, surveillance and communication equipment emergency services like aviation obstruction lights. Adequate levels of lighting levels have been maintained and energy saving luminaries have been installed. Special emphasis has been given to incorporate lighting protection at bridge tower and control room building to protect those building/ structures and the sophisticated monitoring and communication equipment installed therein.
Challenges encountered during execution of the project Engineering challenges BWSL Project is a unique and pleasing structure, but before undertaking the construction, following were the major challenges to be addressed:-
• The foundations of the bridge included 604 large diameter shafts drilled to lengths of 6m to 34m in geotechnical conditions that varied from highly weathered volcanic material to massive high strength rocks.
• The superstructure of the approach bridges were the heaviest spans in the country to be built with span-by-span method using overhead gantry through a series of vertical and horizontal curves.
• A one-of-its-kind, diamond shaped 128m high concrete tower with flaring lower legs, converging upper legs, unified tower head housing the stays and a throughout varying cross section along the height of tower.
• Erection of 20000 MT Bandra cable-stayed deck supported on stay cables within a very close tolerance of deviations in plan and elevation.
The challenges were varied and started right from the Pre-Cast yard.
Ground stabilisation for Pre-Cast Yard The Pre-Cast yard is located on reclaimed land. The yard caters to casting, storing and handling of pre-cast segments for the project totaling 2342 in numbers. The storage capacity requirement of yard is to be about 470nos. As the area available is limited, the segments are to be stored in stacks of three layers. The bearing capacity of the ground is of paramount importance to enable three-tier storage of segments. As the pre-cast area is on reclaimed land, the bearing capacity of existing ground was very poor and found to be less than 2 T/Sqm.
Hence detailed ground stabilization was carried out, which involved following:
• Excavation of the ground to a depth of ~ 2.5Mtrs.
• Strengthening the ground using rubble soling and filling the voids with sand. The soling thus done was compacted layer by layer using vibratory rollers.
• Total area of the Pre-cast Yard was covered with a layer of PCC.
• RCC Footing done to facilitate storing of segments.
These measures offered the required strength to the casting yard. Marine works Foundation and substructure The foundations for the BWSL project consist of 2000-mm diameter piles numbering 120 for the cable-stayed bridges and 1500-mm diameter piles numbering 484 for the approach bridges. The project’s site geology consists of basalts, volcanic tuffs and breccias with some
intertrappean deposits. These are overlain by completely weathered rocks and residual soil.
The strength of these rocks range from extremely weak to extremely strong and their conditions range from highly weathered and fractured, to fresh, massive and intact. The weathered rock beds are further overlain by transported soil, calcareous sandstone and thin bed of coarse grained conglomerate. The top of these strata are overlain by marine soil layer up to 9m thick consisting of dark brown clayey silt with some fine sand overlying weathered, dark brown basaltic boulders embedded in the silt. The major engineering problems that needed suitable solutions before proceeding with the work were as follows:
1. Highly variable geotechnical conditions of the foundation bed as explained above.
2. Highly uneven foundation bed even for plan area of one pile.
3. Presence of Intertidal Zone (Foundation Bed exposed in low tide and submerged in high
tide).
The key to success was a program of pier by pier in-situ testing. An extensive subsurface exploration and drilling program (total 191 bores inside sea) was undertaken to define the subsurface stratigraphy, determine the rock types and obtain material properties for optimizing the foundation design. Owing to a highly variable geology, the design calculations were performed on a pier-by-pier basis and the unit side
shear values were checked that they did not exceed the load test results under similar rock conditions.
The working load on the approach piles ranges from 700 tons to 1500 tons whereas for the piles below the cable-stayed bridge working load is 2500 tons. For conducting the load test on the piles, the load to be applied varied from 4500tons to 9600tons.
Arranging reactions for such loads either by normal kentledge method or by soil anchor required massive scale arrangements in the sea waters. This was completely avoided by a careful planning of load
test using the Osterberg load cell method (Refer sketch 1).
The award winning Osterberg Cell, or “O-Cell’, gets its name from the inventor, Dr. Jorj O. Osterberg. The O-cell is a hydraulically driven, high capacity, sacrificial loading device installed within the foundation unit. Working in two directions, upward against side-shear and downward against end-bearing, the O-cell automatically separates the resistance parameters. By virtue of its installation within the foundation member, the Osterberg Cell load test is not restricted by overhead structural beams and tie-down piles. Instead, the O-Cell derives all reaction from the soil and/or rock system. End bearing provides reaction for the skin friction portion of the O-Cell load test, and skin friction provides reaction for the end bearing portion of the test. Load testing with the O-Cell continues until one of three things occurs: ultimate skin friction capacity is reached, ultimate end bearing capacity is reached, or the maximum O-cell capacity is reached.
Each Osterberg Cell is specially instrumented to allow for direct measurement of the end bearing and skin friction. O-Cells range in capacities from 0.7 MN to 27 MN. By using multiple O-Cells on a single horizontal plane, the available test capacity can be increased to more than 200 MN. At BWSL, four test locations were selected for the following criterion.
Reverse Circulation Drilling method is adopted for foundation construction. The highly uneven foundation beds and the presence of intertidal zone brought in lots of difficulty in terms of Liner pitching. This problem was solved by constructing a gabion boundary at the bed level around the casing, pouring concrete between the casings to make an artificial penetration of the casing. After setting of the concrete under the water, drilling was commenced using RCD.
It is interesting also to mention that loss of water head during continuous drilling operation was a major problem while working in the intertidal zone. This water head loss leads to very slow production rate and very high consumption of drill bits. To overcome this problem, pits
were made in the low tide at each foundation location using an Excavator and the casing was placed at the bottom of the pits. Then the casing was placed in the pits and was concreted to make an artificial penetration, maintaining the proper water head for continuous drilling.
For several locations, cofferdam construction using steel liner and sheet piles, was not possible due to very hard and uneven strata. Here the problem was solved using circular steel caissons. These caissons were fabricated outside and towed to location using A-frame barge. The caissons were sunk at the location using counterweights. The unevenness at the bottom was sealed using the gabion method. The
benefit of this method was that it completely eliminated deployment of resources like Jack up Platform, Crane, Vibrohammer, Compressor, etc for liner pitching. It also eliminated substantial amount of field works and is pre-fabricated in principle. |
Hi
I think this project is a part of the Western Freeway Sea Project, which, in turn, is a part of a larger proposal to upgrade the road transportation network of greater Mumbai.
GPS could play a great role in construction control.
Leave your response!
MY NEWS
Order your FREE copy!
PREVIEW THE BOOK
PREVIEW THE BOOK
________________________________________
The Drone Rules in India 2021
________________________________________
National Geospatial Policy of India 2022
________________________________________
Indian Satellite Navigation Policy – 2021 (Draft)
________________________________________
Guidelines for acquiring and producing Geospatial Data and Geospatial Data Services including Maps
________________________________________
Draft Space Based Remote Sensing Policy of India – 2020
________________________________________
National Unmanned Aircraft System (UAS) Traffic Management Policy – Draft
________________________________________
Advertisement
Interview
Kiyokazu Minami
Secretary General, Executive Director, Japan Institute of Navigation
Member, Leader of GPS/GNSS research group, Japan Institute of Navigation
Easy Subscribe
Previous Issues
Log In
E-ZINE
Partnership
10 - 12 February, 2025
The Queen Elizabeth II Centre, London
1-3 April
Porto, Portugal
9-10 April 2025
Singapore
23-24 April 2025
Washington DC, USA
5 - 6 May 2025
Jeddah, Saudi Arabia.
12-14, May
Ottawa, Canada
21-23, May 2025
Wrocław, Poland
4 - 5 June
London, UK
8-12 September
Baltimore, USA
21 - 24 September 2025
Baška, Krk Island, Croatia
3-5,November
Calgary, Canada
3-5 November 2025
Florianópolis, Santa Catarina, Brazil
21-23 May
Benidorm, Spain
View Past Events