
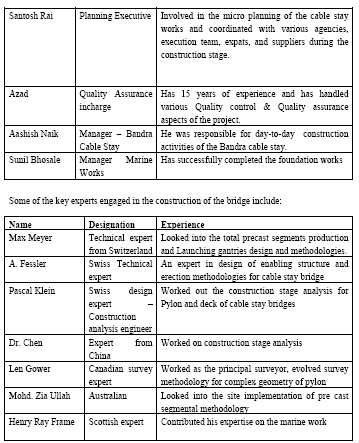
Partners involved
1. VSL Singapore Pvt Ltd : Technical Consultants
2. Ultra Tech : Supplier of cement
3. Metco group of companies: Supplier of bearings
4. Tata Steel, RIN Ltd & SAIL: Supplier of steel
5. ELKEM International Ltd.: Norway-based company supplier of micro silica
6. SPCC: China-based company supplier of stay cable
7. DOKA Australia: supplier of Plyon fromwork
Equipment used
The major equipments deployed for this project are:
• Jack up platform, launching truss, reverse circulation drilling machine floating barrages,
boats, crawler crane, tower crane, gantry crane, derrick crane, placer boom, diesel
generators, concrete pump, transit mixers & ‘A’ frame barrage.
• The equipment was brought together from various countries.
The construction of the mammoth bridge structure required huge cranes and other structures
to lift material for off shore and on shore structures. Some of these included:
1. Launching Truss: Weighing 1250 tonnes and measuring 112 m in length, it was used for
lifting segments each weighing 130 tonnes. This has been fabricated in India.
2. Jack up platform: Size 18.3x30x2.1m (Width x Length x Depth) having four legs of
30m. It is a floating equipment used for marine work.
3. Flat barge: Size 30x12x2m. Like motor boats, they are driven inside the sea for material
transportation.
4. Self-propelled barge: It is a barge with a machine component and is used for concrete
transportation.
5. Crawler crane: Capacity ranges from 75-150 tons. It is used for material and heavy
lifting activities.
6. RCD drill bit: Dimension 1.5m x 2m diameter. Imported from Korea, the RCD drill bit
is used for pile drilling work.
7. Vibro hammer (PTC): Imported from France and used for driving of steel liners.
8. Fushun crawler crane: Imported from China, Capacity 80 tons.
9. NCK Eiger crane: Imported from England, capacity 65 tons.
10. Kobelco crawler crane: Imported from Hong Kong, capacity 150 tons.
Fascinating facts
• The project has already been acclaimed by the viewers as an engineering marvel of
modern India.
• First Cable-Stay Bridge in India in open sea.
• The length of the bridge is 63 times the height of the Qutub Minar in Delhi.
• Its weight is equivalent to 50,000 African elephants.
• The length of the steel wires used is equivalent to the circumference of the earth.
• The height of the cable-stayed tower is 128 m, which is equal to a 43-storey building.
• A total of 424 cables were used for both Bandra cable stay as well as Worli cable stay
bridges.
• The cables have been sourced from Shanghai Pujyang Cable Company, China. The cables
were subject to a series of quality and engineering tests to meet the special requirements
including fatigue tests of two million cycles.
• The cables are made of high tensile steel and are designed to take the maximum load of
900 tons.
• 92,000 tons of cement was utilized to make BWSL.
• Environment friendliness was top priority during the construction – fly ash, a waste
product extracted from thermal power plants, was mixed with concrete, to make the
construction durable as well as eco-friendly, thus making good use of waste material.
• The construction team is like a mini United Nations: several teams of foreign engineers
and technicians have worked on specialized tasks on the structure; these include
professionals from China, Egypt, Canada, Switzerland, Britain, Serbia, Singapore,
Thailand, Hong Kong, Indonesia and the Philippines, Australia.
• The Launching Trusses, each 112 meters long, were custom built to precision by HCC for
this project. The pre-cast concrete segments of this four-lane road are fabricated at the
Bandra site location. These segments are then carried on a barge to the construction
location and are lifted by the Launching Truss to the designated height and assembled
between two piers, each 50 meters apart. Fifteen such segments are fitted between two
piers and the Launching Truss can lift all fifteen segments together, weighing 130 tons
each, between two piers. Once these segments are fixed between two piers, the Launching
Truss crawls to the next piers on its mechanical legs.
• Given the gigantic size of the project, mega equipments were used in construction;
bringing them to the project site and operating them was a feat in itself. Asian Hercules,
one of the biggest floating shear leg cranes in the world, was hired from Singapore to lift
the massive 1250 tonnes, custom-built Launching Trusses with its mechanical arm and
relocate them on the Worli side of the bridge.
Hindustan Construction Company (HCC)
1. VSL Singapore Pvt Ltd : Technical Consultants
2. Ultra Tech : Supplier of cement
3. Metco group of companies: Supplier of bearings
4. Tata Steel, RIN Ltd & SAIL: Supplier of steel
5. ELKEM International Ltd.: Norway-based company supplier of micro silica
6. SPCC: China-based company supplier of stay cable
7. DOKA Australia: supplier of Plyon fromwork
Equipment used
The major equipments deployed for this project are:
• Jack up platform, launching truss, reverse circulation drilling machine floating barrages,
boats, crawler crane, tower crane, gantry crane, derrick crane, placer boom, diesel
generators, concrete pump, transit mixers & ‘A’ frame barrage.
• The equipment was brought together from various countries.
The construction of the mammoth bridge structure required huge cranes and other structures
to lift material for off shore and on shore structures. Some of these included:
1. Launching Truss: Weighing 1250 tonnes and measuring 112 m in length, it was used for
lifting segments each weighing 130 tonnes. This has been fabricated in India.
2. Jack up platform: Size 18.3x30x2.1m (Width x Length x Depth) having four legs of
30m. It is a floating equipment used for marine work.
3. Flat barge: Size 30x12x2m. Like motor boats, they are driven inside the sea for material
transportation.
4. Self-propelled barge: It is a barge with a machine component and is used for concrete
transportation.
5. Crawler crane: Capacity ranges from 75-150 tons. It is used for material and heavy
lifting activities.
6. RCD drill bit: Dimension 1.5m x 2m diameter. Imported from Korea, the RCD drill bit
is used for pile drilling work.
7. Vibro hammer (PTC): Imported from France and used for driving of steel liners.
8. Fushun crawler crane: Imported from China, Capacity 80 tons.
9. NCK Eiger crane: Imported from England, capacity 65 tons.
10. Kobelco crawler crane: Imported from Hong Kong, capacity 150 tons.
Fascinating facts
• The project has already been acclaimed by the viewers as an engineering marvel of
modern India.
• First Cable-Stay Bridge in India in open sea.
• The length of the bridge is 63 times the height of the Qutub Minar in Delhi.
• Its weight is equivalent to 50,000 African elephants.
• The length of the steel wires used is equivalent to the circumference of the earth.
• The height of the cable-stayed tower is 128 m, which is equal to a 43-storey building.
• A total of 424 cables were used for both Bandra cable stay as well as Worli cable stay
bridges.
• The cables have been sourced from Shanghai Pujyang Cable Company, China. The cables
were subject to a series of quality and engineering tests to meet the special requirements
including fatigue tests of two million cycles.
• The cables are made of high tensile steel and are designed to take the maximum load of
900 tons.
• 92,000 tons of cement was utilized to make BWSL.
• Environment friendliness was top priority during the construction – fly ash, a waste
product extracted from thermal power plants, was mixed with concrete, to make the
construction durable as well as eco-friendly, thus making good use of waste material.
• The construction team is like a mini United Nations: several teams of foreign engineers
and technicians have worked on specialized tasks on the structure; these include
professionals from China, Egypt, Canada, Switzerland, Britain, Serbia, Singapore,
Thailand, Hong Kong, Indonesia and the Philippines, Australia.
• The Launching Trusses, each 112 meters long, were custom built to precision by HCC for
this project. The pre-cast concrete segments of this four-lane road are fabricated at the
Bandra site location. These segments are then carried on a barge to the construction
location and are lifted by the Launching Truss to the designated height and assembled
between two piers, each 50 meters apart. Fifteen such segments are fitted between two
piers and the Launching Truss can lift all fifteen segments together, weighing 130 tons
each, between two piers. Once these segments are fixed between two piers, the Launching
Truss crawls to the next piers on its mechanical legs.
• Given the gigantic size of the project, mega equipments were used in construction;
bringing them to the project site and operating them was a feat in itself. Asian Hercules,
one of the biggest floating shear leg cranes in the world, was hired from Singapore to lift
the massive 1250 tonnes, custom-built Launching Trusses with its mechanical arm and
relocate them on the Worli side of the bridge.
Hindustan Construction Company (HCC)
Meeting challenges with innovation!
Col S Diwanji
Project Manager,
Bandra-Worli Sea Link Project,
Hindustan Construction Company
satish.diwanji@hccindia.com
|
When did the work on the Bandra-
Worli Sea Link project start?
Hindustan Construction Company
(HCC) was awarded Package IV
of the Project and work started in
September 2000, but was held up
due to several reasons including
environmental issues and protests
by fishermen. In right earnest the
work started in December 2004.
On what basis was the distance
between the piers and the height
of the bridge decided?
The span between the piers is 50m. This
distance was arrived at after considering
various factors, which included
optimization between the foundation
cost vs. the superstructure cost. If the
piers are wide apart then the foundation
cost comes down, but the superstructure
becomes heavier and its cost goes up.
Also the navigational requirements
as in an emergency the smaller
trawlers and boats should be able to
pass between the piers. Moreover,
more number of piers provide better
wind resistance to the bridge.
Why was the cable stayed bridge design
chosen for the Bandra-Worli Sea Link?
A cable stayed design has some inherent
advantages compared to other conventional
designs, the main being that it allows
for larger spans. There were three main
reasons why a large span was needed in
case of the Bandra-Worli Sea Link:
• A navigational channel for the
fishermen and other sea faring
vessels had to be maintained.
• There are plans to expand
the present jetty.
• There are overseas communication
cables on the seafloor which
keep shifting and this had to
be taken into consideration.
At what stage of the bridge
construction was the need for
precision survey instruments felt ?
We knew from the start of the project that
high precision equipment would be needed
and one of the first things we did was
to mobilise the Total Stations – the first
of which were procured in early 2001.
|
Survey Challenges! Bandra Worli Sea Link Project
Len Gower, Principal Surveyor on the Bandra-Worli Sea link Project for Hindustan Construction Company, shares his experiences on the project in an exclusive interview with Coordinates. |
Len Gower
len.gower@gmail.com
|
1. For those of us who use them, a bridge is a bridge; but for those who build them each bridge has its individuality. Please tell us about some of the bridges that you have worked on in the last few years.
In the past 10 years, I have worked on 7 long span bridges. Each one posed unique technical challenges that were overcome by my teams.
The Rion Antirrion Bridge, between the Peloponnese peninsula and the Greek mainland, is a four pylon, 2200 metre span across a seismic fault in the Strait of Corinth. The pylon bases are not fixed to the seabed, but rather rest on an engineered bed of gravel and inclusion pipe piles. Thus they are free to move during a seismic event, without sustaining damage. The deck is mounted to the pylons with telescopic ‘shock absorber’ energy dampers, so minor pylon movement can be accommodated safely.
The Puente de las Americas cable stayed bridge spans the Panama Canal, about 15 km east of Panama City. The size of the ships that pass through the canal necessitated a very high navigation envelope beneath the deck, and the commercial ramifications of interrupting canal traffic meant that the entire bridge had to be constructed without the use of marine barges or floating cranes. The deck was cast in situ with movable shutters and one of the largest formwork travellers ever utilized in bridge construction. The other major technical challenge was that the deck erection started before the pylon construction was complete. This meant that if the deck was out of balance for some period of time, the pylon lifts had to be cast ‘out of plumb’ with the embedded cable anchors still set to tight angular tolerances.
The Cooper River Bridge in Charleston, South Carolina was (at the time) the longest cable stayed bridge in North America. The slenderness of the pylon legs and the lack of a cross beam below the cable anchorages made pylon leg construction a challenge. The selection of PERI self climbing formwork made it impossible to place an instrument bracket on the formwork support frame, so we employed a Trimble DGPS solution. Early in the morning, immediately after a section of the pylon leg was cast, with the concrete in place for 4-6 hours, we installed a special instrument pedestal onto a ‘cast in’ pipe flange. The tower crane picked up a 15 ton test block (to make the mast load neutral) and then swung to a position that permitted the GPS receiver to receive the maximum number of ‘clean’ satellite signals. We used a set of three ‘one minute’ static position averages, capturing one position every second, to determine our XY position and an approximate Z. We corrected the weaker Z position by taping a ∆elevation up from the previous lift. We then replaced the GPS antenna with a Leica total station and obtained an angular orientation from a back sight, set about 2 km away. We set two auxiliary instrument brackets on the inside face of the exposed cable anchor box, and then surveyed their positions for use in a 3Dimensional ‘Best Fit’ solution.
The actual as-built of the most recently cast lift took place 3-4 hours later, long after sunup and with the tower crane in full operation, but we could use a least squares solution to correct for temperature gradients and eccentric load induced tower deflections by turning off the internal compensators, observing the auxiliary bracket positions again, then taking measurements to our concrete lift as-built positions last. During post processing, we applied a 7 parameter similarity transformation to the observed data to perform the scale factor, rotations and transformations necessary to get the instrument position and the auxiliary bracket positions to match the 06:00 AM positions, before sunup and with the tower crane neutral. These transformation parameters were of course applied to the as-built measurements, to convert them to 06:00 AM readings.
The Shaikh Zayed Bridge was not a cable stayed bridge, but rather a cast in place concrete deck supported by cable stays from a series of asymmetrical steel arches. This project was designed by Zaha Hadid, engineered by HPR and proved to be almost un-buildable, and absolutely unprofitable for the main contractor. It is currently 2 years behind schedule, with about 18 months to go until completion. I stayed on this project only until I found an exit strategy – the Sutong Bridge, in Nantong PRC.
The Sutong Bridge is currently the world’s longest cable stayed bridge, with a clear span length of 1088 metres! By comparison, the Bandra Worli’s main span is 500 metres. Ultra long span bridges bring a myriad of technical challenges, which directly impact the project costs and construction schedule. Long decks require tall towers (to be able to accommodate the increased number of stay anchors, and still maintain the necessary angular cable geometry). Sutong’s pylons were 306 Metres in height, as compared to Bandra Worli’s tallest pylon at P19, at 124 Metres. The crossing of the Yangtze River, between Nantong and Suzhou has strong winds during most of the year so deck flutter and tower deflection were much more of a problem than thermal gradient induced deflections. The pylons were so tall, that after 200 metres, two auxiliary instrument positions had to be transferred onto the pylon, to perform set out and as-built surveys, similar to the Cooper River Bridge, however the Chinese chose a more traditional approach – a reciprocal observation procedure with a Leica 2003 total station. The rebar for the lifts above were much too tall to permit a GPS antenna to receive satellite data free from multi-path errors.
The anchor boxes for the pylons were fabricated close to Beijing, and then barged down to Nantong. These boxes were quite similar to the Bandra Worli boxes, and the survey control methodology chosen was mine, a combination of metrology and steel fabrication ‘dimensional’ quality control. The only serious challenge in anchor fabrication is to achieve angular accuracy in the three planes (α, β and g), AFTER the welding is completed. Anticipating angular errors due to weld shrinkage, and mitigating unexpected results is almost an art – not a science. If the acceptance criteria for angular errors is +- 0.5 degrees (fabrication and installation errors combined) that means that the post weld fabrication error must be between +- 0.25 degrees and the pre-weld fit-up errors between +- 0.125 degrees. In an anchor plate of 400x400mm, that means making repeatable survey measurements of sub-millimetre accuracy. This level of accuracy demands the best 1st order instrumentation, on-board software, customized targeting and methodology available. Both the Nantong and the Bandra Worli anchor boxes were manufactured and installed within the designer’s tolerances.
I also consulted to a bridge project in Canada, a long floating bridge in the province of British Columbia. The challenge they faced that prompted my involvement was completing the pylon leg construction once the pontoons were afloat. Again, I designed a system based on a 7 parameter similarity transformation, utilizing a total station that could operate with the internal compensators deactivated, and a series of control points originally established when the pontoon was still in the dry dock.
2.Could you please tell us briefly how a cable stayed bridge is different from other bridges?
Cable stay supported bridges are a type of suspension bridge. A typical suspension bridge, like the Golden Gate Bridge in San Francisco, consists of two large diameter incrementally spun cables, hanging between the two main towers, on a catenary, with much smaller diameter vertical hangers spaced evenly along the deck, connected to the suspension cables.
Cable stayed bridges have many smaller diameter cables, connecting the pylon legs to the deck at evenly spaced intervals. The pattern of pylon connection can vary. The parallel stay system is called a ‘harp’, the system that bunches the pylon anchors close to the top of the pylon is called a ‘fan’, but the most common style is to space the anchors from the pylon top downwards towards the deck. This system is called a modified fan.
The longest spans still require a suspension bridge, but for the medium spans (100 – 1000 metres), cable stayed bridges may offer cost benefits and shorter construction schedules to the client.
The suspension bridge needs large, expensive abutments to ‘anchor’ the suspension cables, and the time it takes to spin the suspension cables is lengthy. If the span distance permits, a cable stayed bridge alternative offers about 12 months gain in the schedule, as no spinning delays are required. A possible compromise is a hybrid design, where a portion of the bridge deck is partially suspended by cable stays, while the suspension cable is being spun, and then upon cable spinning completion, the mid span portion of the deck is suspended by hangers from the catenary cables. The cost benefit is slight with this alternative, so is rarely chosen. Multiple span cable stayed bridges are also a cheaper alternative for long span bridge designers, such as the Rion Antirrion Bridge in Greece. The minor drawback to this solution is that the navigational channel is cut into smaller portions by the extra pylons.
3.Please tell us about some of the survey related challenges you faced on the Bandra Worli Sea Link Bridge?
The survey related challenges for the Bandra Worli were similar to most cable stayed bridges. The accuracy requirements are always demanding, especially in the fabrication of the cable anchor assemblies. The angular misalignment permitted is+- 0.5 degrees in the completed structure, so the fabrication and assembly tolerances are much tighter. We fabricated the bearing plate / guide pipe assemblies to +- 0.06 degrees from perpendicular. We placed them in the deck slab formwork (prior to concrete placement) within +- 0.125 degrees, to ensure that they would still be within +- 0.25 degrees after the concrete had been placed and the concrete curing shrinkage was complete. This procedure required custom design / manufacture of very accurate bearing plate/pipe sleeve assembly jigs, as well as special dual turnbuckle pipe sleeve support yokes and customized targeting and tooling for surveying the anchor assemblies in the deck sections.
The fabrication of the pylon head anchor boxes was even more complex, as weld shrinkage had to be anticipated, and unforeseen results dealt with during erection. The size of the base plate that the bearing plate rests on is only 700x400 mm in dimension, so that means the fit-up survey measurements had to be accurate to sub-millimetre, to ensure the 0.125 degree angular misalignment specification was met.
The pylon legs (below the tower head) were very slender, so were susceptible to thermal gradient deflections. Care had to be taken to ensure that all important surveys were performed in a thermally neutral state. The legs also deflected towards the pylon centre after concrete placement, so the ‘as-set’ positions were always different from the ‘as-built’ positions.
The reference geometry supplied by the designer is based on Time ∞, whereas we were constructing every element at Time 0, so allowances had to be made for future creep, shrinkage and elastic shortening. These allowances are referred to as pre-cambers and over heights/lengths. For example, the over height for the P19 pylon’s tower head was +35 mm. As we completed the south carriageway first, the deck load was transferred into the pylon legs, causing the shared centre legs to shorten less than the single outer leg. This caused the pylon to temporarily incline away from bridge centreline by nearly 30 mm at the top of the tower head. This meant that we had to construct the north pylon’s tower head on a similar inclination, with the expectation that the pylon would come back to plumb when the load of the north deck was in place, bringing the pylon sub structure and common foundation back into equilibrium.
4.Could you please elaborate on the role of the pylons in a cable stayed bridge and the survey methodology that was used to put them up in the Bandra Worli Sea Link Bridge?
The pylons of a cable stayed bridge are used primarily to anchor the upper cable stay sockets. Many times the deck is firmly attached to the pylons (as in the case of the Bandra and Worli spans) but other bridges only have sliding pot bearings at the pylons (Ting Kau Bridge, in Hong Kong), or elastomeric bearings between the tower’s cross beam and the underside of the deck (Alex Fraser Bridge, Cooper River Bridge).
The pylon must be tall enough to provide sufficient space for all the cable anchors, and still yield a decent vertical angle at the uppermost cables. Obviously, as the alpha angle decreases with the height of the anchor above the deck, the amount of cable force in the vertical direction decreases as the force in the horizontal direction increases. This is why the diameter of the longest cables is greater than those nearest the pylon (with the steepest alpha angles). They have to be strong enough to resist the extra cable force applied, to yield sufficient upward lift to support the dead load and the live load (traffic) in the worst case scenario.
The survey method utilized to construct the Bandra Worli pylons was based on the fact that the pylon legs were inclined. Inclined pylon legs pose a significant challenge to the contractor, as the rebar cage will have a natural tendency to sag down hill during construction. If a rebar cage sags, it will be out of tolerance when completed and clash with the formwork adjustment procedure during the final as-set survey. Our solution was to implement a sacrificial rebar template assembly, to guide the construction of the rebar cages and to ensure that there would be no clashes of the steel embedments, like crane tie-ins and DOKA climbing cones.
Our surveyors set the rebar templates in the early morning hours, after the self climbing formwork was fixed for the next lift. These templates had 3 or 4 key points stamped onto them that the surveyors could shoot, and once the support framework was completely interconnected, formed a local survey network that moved with the pylon’s thermal deflections, yet was still based on a thermally neutral pylon. At any time, and with any amount of pylon leg deflections present, our surveyors could set up their instrument on the special brackets attached to the DOKA framework, disable the internal compensators and then perform a ‘resection’ or ‘free station’ operation to determine instrument co-ordinates and orientation, for set-out work. Once the concrete was placed, the pylon would deflect downwards towards the bridge centreline, so new co-ordinates of the rebar template were measured (again in the early hours of the morning). The instrument was again transferred up to the top of the pylon, installed on the same bracket, where the as-built survey could be completed quickly and accurately.
The main challenge to these surveys was in the formwork construction. On most bridge pylons, there are 2 fixed panels and two adjustable panels, so fine adjustment at each corner is possible. For the Bandra Worli pylons, the formwork had no adjustability. Each panel butted up to the adjacent panels, so the entire shutter assembly acted as a solid body. To move the top into position, the entire shutter had to be tipped, similar to the survey alignment procedure of an elevator core shutter. If an error in a panel length cutting operation occurred, there was no way to eliminate this. Small errors could be mitigated by setting the shutters so that half the error was on one corner and the other have was on the opposite corner. Our survey alignment criteria was therefore based on the centroid of the entire shutter (6 point average in the pylon leg sections & 12 point average in the tower head sections), and not on individual corner positions.
5.In the Bandra Worli Sea Link project what were the phases in the construction where survey played a critical role.
The phases of construction most dependent on survey were the following:
- Offshore pile driving, cofferdam placement and marine foundation construction
- Deck segment match casting
- Deck segment installation
- Pylon leg casting
- Pylon leg junction below the tower head
- Cable anchorage fabrication
- Tower head anchor box fabrication
- Tower head installation
- Deck profile surveys
- Wet joint alignment between 16 deck segment ‘blocks’
- Deck closure surveys, pre cable length fine tuning
- Post fine tuning deck profile surveys
- Kerb and asphalt grades
6. What kinds of survey instruments are best suited for the different survey works in a typical cable stayed bridge construction.
The best instruments for cable stayed bridge surveying are state of the art, high accuracy, vibration tolerant electronic total stations, with ATR (automatic target recognition) and on-board software for Free Station and Resection.
GPS receivers can also play a role, when the pylons are extremely tall (as in the Millau Bridge in France) or far out to sea. Their lack of accuracy in Z measurements is their only weakness, in my opinion. With improvements in multi-path error mitigation and the implementation of the Glonass satellites, the availability issue and PDOP are much improved.
The exception to this high tech equipment is utilizing a pair of old fashioned tilting levels to perform accurate deck profiles. The vibrations present in cable stay supported decks makes internally compensated survey equipment susceptible to ‘compensator excitation’, producing a blurred image of the crosshairs in an auto level or randomly inaccurate vertical differences in total stations. A split bubble tilting level exhibits the deck vibrations in the movement of the tilting bubble – while the cross hair image remains completely stable. By adjusting the level so as to balance the bubble movement evenly, a level observation is possible. The purpose of having two instruments observing a single staff is that long circuits can be run ‘one way’. Each set-up produces two back sights and two foresights, so constitutes a closed level loop. The next set-up again produces 2 back sights and two foresights, which is again a closed loop. It is like building a chain, link by link. It was quite common to be able to level from P17 to P21, a distance of 600 Metres, with a misclosure of only 1-2 mm.
7.Could you tell us about the kind of accuracies that are needed for various aspects of a cable stayed bridge?
There are many different accuracy requirements, in the steel fabrication/concrete casting and their related survey control measurements, as some types of errors can propagate or systematically multiply and others are essentially ‘one off’ – with no knock-on effects.
Deck segment lengths are a typical dimensional component that has potential for systematic error propagation. A +1mm error on every 3M long deck segment of a 600 metre span will produce +100 mm errors at each expansion joint at the end spans, or roughly 10% of the thermal gradient expansion range. This is still an acceptable range of error, but 200 or 300 mm wouldn’t be, so deck lengths have to be measured accurate to the millimetre, and significant errors must be tracked during deck segment installation, and compensated for in the last in situ stitch joints cast.
Installation of the first deck segment of a 16 segment block is another example of a potential systematic error situation. For every 1mm rotational error (in either the horizontal or vertical directions) there will be a 16mm error at the next wet joint. When setting these segments during wet joint construction, we measure the horizontal positions to the millimetre and the vertical differences to better than 0.5 mm.
Cable anchorage placement errors in either the deck or pylon are minor, as there is usually a fairly generous range of cable length adjustment at the live end socket – either by split shims or by threaded sockets and lock nuts. A shift of 1 or 2 centimetres in longitudinal or transverse directions is insignificant, so normal survey procedures are quite capable of controlling installation and identifying absolute errors. The exception to this is angular misalignments. The principal of multi-strand stays, or parallel wire pre-formed stays is that each wire or strand carries an equal proportion of the cable force. If the bearing plate isn’t perpendicular to the cable force vector, then some wires will carry much more of their respective share of the force, and other wires will carry much less of the force. The over-stressed wires are therefore susceptible to premature fatigue failures. Most manufactures will provide a warranty period for their stays, providing the final angular alignments are within +-0.01 Radians (+- 0.57 degrees). Even with this ‘less than generous’ installation tolerance, longer guide pipes with a misalignment close to the limit will pose problems during damper installation. This is the one phase of works that requires the best survey equipment and methodology available, to produce repeatable measurements at sub millimetre accuracy.
The actual positions of the anchors need to be measured accurately, only IF the cables are to be installed to length, instead of force. As absolute cable lengths at the installation forces are very difficult to determine, engineers rarely use length as an installation criteria, and instead choose force (as measured at the hydraulic jack pump). As long as the cable anchor socket has sufficient capacity for minor length errors, the cable length, deck anchor and pylon anchor locations need only to be within 2 cm of design.
Pile driving and coffer dam positioning can be performed to +- 5mm without any detrimental effects, so is a perfect application for DGPS.
8.How important is the use of GPS for survey purposes in a cable stayed bridge project? How was it used in the Bandra Worli Sea Link Bridge project.
The application of GPS in cable stayed bridge construction is quickly gaining acceptance, for specific tasks. While it can’t replace all traditional survey equipment – it does have cost benefits in certain applications.
Bridges far from shore, very tall pylons, marine plant positioning, bathymetric vessel positioning, and construction site control networks are all perfect applications for DGPS. You can even use static GPS receivers for as-builts, provided the Z co-ordinates are not critical.
In dynamic structures that require periodic monitoring, a DGPS system that logs reading once per second, over 24 hours is a much more cost effective solution than a two man crew with a total station and prism pole.
As the Bandra Worli Bridge is fairly close to shore, GPS played a limited role in construction control.
|