Mumbai: the financial capital of India.
A tiny island bursting at the seams
with its teeming millions. With real estate
prices among the highest anywhere in
the world, land is an extremely precious
commodity in the city. Expanding the
existing infrastructure especially transport
has been a nightmare for the city planners.
But, one thing that Mumbai does have
plenty of is the sea – surrounding the
island on three sides. Finally when push
came to shove, with the only connection
between the western suburbs and ‘town’
- the Mahim causeway choked to its
limit, the planners looked out to the sea.
The idea about a bridge in the sea seemed
far fetched at first, but where there is a will
there is a way. Many years in the planning
and more years in the making, but finally
Mumbaikers can now speed across the
Mahim bay on a swanky new 8 lane 4.7
km bridge, cutting the earlier travel time
of up to 60 minutes to just 15 minutes.
The marvel that has brought this sea
change to the life and landscape of
Mumbai is the Bandra-Worli Sea Link –
the first ever sea link to be built in India.
The Bandra-Worli Sea Link (BWSL) is a
part of the Western Freeway Sea Project,
which, in turn, is a part of a larger proposal
to upgrade the road transportation network
of greater Mumbai. The project has
been commissioned by the Maharashtra
State Road Development Corporation
Ltd (MSRDC) and the Maharashtra
Government and has been built by
Hindustan Construction Company (HCC).
The entire project was originally conceived
as one large project comprising, different
components, but in order to accelerate
the overall construction schedule, the
project was divided into five construction
packages. Four of these packages involved
work on the island, while one – Package
IV involved construction in the sea.
“Package IV”
The largest and main phase of Bandra-
Worli Sea Link Project was Package IV
which included the construction of Cable-
Stayed Bridges together with viaduct
approaches extending from Worli up to the
Toll Plaza at Bandra end and an Intelligent
Bridge System (IBS). The work under
this package was awarded to HCC.
The Bridge
The bridge consists of twin continuous
concrete box girder bridge sections for
traffic in each direction. Each bridge
section, except at the cable-stayed
portion, is supported on piers typically
spaced at 50 meters. The bridge layout
is categorized into three different parts:
• Part 1 - The north-end approach
structure with Pre-Cast (PC)
segmental construction.
• Part 2 - The Cable-Stayed Bridge at
Bandra channel is with 50m -250m-
250m-50m span arrangement and
the Cable-Stayed Bridge at Worli
channel is with 50m-50m-150m-
50m-50m span arrangement.
• Part 3 - The south end approach
structure with Pre-Cast
segmental construction.
Toll Plaza
A modern toll plaza with 16 lanes
is provided at the Bandra end. The
toll plaza is equipped with a stateof-
the-art toll collection system.
Intelligent Bridge System
The intelligent bridge system provides
additional traffic information, surveillance,
monitoring and control systems. It
comprises CCTVs, traffic counting and
vehicle classification system, variable
message signs, remote weather information
system and emergency telephones.
The marvel in the making
When one sets out to achieve a first,
the challenges are bound to be many.
Some problems on the project were
unique and needed special solutions,
while other problems were those faced
on any other such project around the
world. The project team of over 3000
workers, HCC engineers, foreign
engineers and technicians met the
challenges head on and overcame them
to give Mumbai its latest landmark.
Foundation and Substructure
The project’s site geology consists of
basalts, volcanic tuffs and breccias with
some intertrappean deposits. This highly
variable geotechnical condition of the
foundation bed in the intertidal zone
needed suitable solutions solutions to lay
the foundation and the substructure.
The foundations for the BWSL project
consist of 2000-mm diameter piles
numbering 120 for the cable-stayed bridges
and 1500-mm diameter piles numbering
484 for the approach bridges. The key
to success was a program of pier by pier
in-situ testing. An extensive subsurface
exploration and drilling program (total 191
bores inside sea) was undertaken to define
the subsurface stratigraphy, determine the
rock types and obtain material properties
for optimizing the foundation design.
The working load on the approach
piles ranges from 700 tons to 1500 tons
whereas for the piles below the cablestayed
bridge working load is 2500 tons.
For conducting the load test on the
piles, the load to be applied varied
from 4500tons to 9600tons. This was
accomplished by a careful planning of load
test using the Osterberg load cell method.
The award winning Osterberg Cell, or
“O-Cell”, gets its name from the inventor,
Dr. Jorj O. Osterberg. The O-cell is a
hydraulically driven, high capacity,
sacrificial loading device installed within
the foundation unit. Working in two
directions, upward against side-shear
and downward against end-bearing,
the O-cell automatically separates the
resistance parameters. By virtue of its
installation within the foundation member,
the Osterberg Cell load test derives all
reaction from the soil and/or rock system.
Load testing with the O-Cell continues
until one of three things occurs: ultimate
skin friction capacity is reached, ultimate
end bearing capacity is reached, or the
maximum O-cell capacity is reached.
At BWSL, four test locations were
selected. Reverse Circulation Drilling
method was adopted for foundation
construction. The highly uneven foundation
beds and the presence of intertidal zone
brought in lots of difficulty in terms of
Liner pitching. This problem was solved
by constructing a gabion boundary at
the bed level around the casing, pouring
concrete between the casings to make an
artificial penetration of the casing. After
setting of the concrete under the water,
drilling was commenced using RCD.
For several locations, cofferdam
construction using steel liner and sheet
piles was not possible due to very hard
and uneven strata. Here the problem
was solved using circular steel caissons.
These caissons were fabricated outside
and towed to location using A-frame
barge. The caissons were sunk at the
location using counterweights. The
unevenness at the bottom was sealed
using the gabion method. The benefit
of this method was that it completely
eliminated deployment of resources like
Jack up Platform, Crane, Vibrohammer,
Compressor, etc for liner pitching. It also
eliminated substantial amount of field
works and is pre-fabricated in principle.
Superstructure
The BWSL Project has (9+2) approach
bridge modules. These modules range from
3 continuous span units to 8 continuous
span units. The deck of the carriageways
consists of triple cell precast box girders
supported on piers founded on independent
substructure. The Concrete Grade for
the superstructure is M60. The average
weight of the span is 1800 tons, whereas
the heaviest span in the bridge weighed
2000 tons. In addition, the trusses were
designed to receive the segment from
the already erected deck as well as from
barges parked directly under the truss.
The erection gantry was a 1260MT
truss designed to erect spans for the
superstructure configuration. The unique
feature of the truss was the maximum
span weight it could handle and that it
could launch the pier and EJ segment
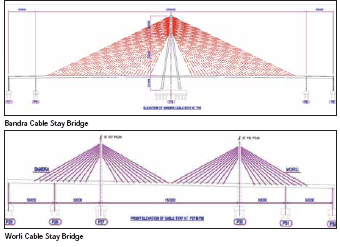
Facts not fiction
• India’s fi rst bridge to be constructed in
open-sea conditions.
• 2342 pre-cast segments for total bridge
with varied width.
• 40,000 MT of reinforcement, 23,0000
cum of concrete, 5,400 MT of Post
tensioning
strands and bars used.
• Osterberg cell technology used for the
first time in India to check pile strength.
• Engagement of Asian Hercules for
shifting 1,260 MT launching truss from
Bandra end to Worli end of the main
cable stay bridge.
• Largest span for cable-stayed bridge in
India.
• Up to 25-m high pier in open sea, giving
ample headroom to marine traffic.
• Use of Polytron Disc in bearings on piers
for the first time in India. |
itself. The truss also had the capacity to
align the total span in hanging condition
after the gluing was completed. The truss
was fully mechanized for self launching
and aligning. An individual segment
could be aligned on the truss using a set
of four hydraulic jacks mounted on each
suspension frame. In order to eliminate the
casting or erection errors within a span,
two wet joints were provided on either
end of the span. The wet joints were cast
after finalization of the span alignment.
A Typical 50m span of the approach
bridges comprises 15 field segments, a
Pier segment and 200mm (nominal) in-situ
wet joints. During the span construction,
all field segments were suspended from
the Gantry, glued and temporarily stressed
together. Once the gluing operation was
The pylon challenge
• The section decreases gradually with
height.
• There are horizontal grooves at every 3m
height and vertical grooves for circular
portion that required special form liners
as well as required attention for deshuttering.
• The tower legs are inclined in two
directions, which created complexities in
alignment and climbing of soldiers.
• Construction joints were permitted only
at 3m level. Inserts were permitted only
in horizontal grooves provided at 3m
height.
|
“This project gave us an opportunity to
showcase our equipment”
Rakesh Kaul
says Rakesh Kaul,
General Manager, Elcome
Technologies Pvt. Ltd.,
with reference to the
survey equipment that
they supplied for the
Bandra-Worli Sea Link.
|
When did Elcome Technologies first
get associated with HCC on the
Bandra- Worli Sea Link Project?
Leica equipment has been used
on most of the Sea Link projects
around the world and based on this
experience we approached Hindustan
Construction Company (HCC)
sometime at the end of 2000 with our
range of specialised equipments for
the Bandra-Worli Sea Link (BWSL).
The first Leica Total Station was
supplied by us to HCC in early 2001.
What were the equipment
supplied for this project?
To meet the demand for high accuracy
coordinate measurements on the BWSL
project we supplied high performance
Leica Total Stations including the TCA
2003, the TCA 1800, the TCA 1201, the
TCRM 1201 R 300 and the TC 1800. We
also supplied the SR 510 GPS equipment.
What kind of support did you
provide HCC vis-à-vis the equipment
that you supplied to them?
We gave comprehensive application
trainings at their site towards effective
and optimal usage of the equipment.
Moreover, these equipments in keeping
the desired accuracies that are required
for such a project, needed timely
calibration checks and corrections – for
this, besides providing them complete
service support during the warranty,
we also got into annual maintenance
contracts for these equipment post their
warranty period. We were thus able to
provide timely service and calibration
of the equipment at our service centre.
Do you think being associated with the
project gives Elcome Technologies any
leverage for other similar projects?
It has been a privilege to be associated
with BWSL and the HCC team we
worked with. Moreover the challenges
in geometric control on the project were
highly demanding and exacting. This
gave us an opportunity to showcase
our equipment and our expertise.
Our experience with BWSL project
will be a basis for us to promote our
technology on other such projects too.
|
completed,
span alignment to the Piers
was followed. After alignment, the wet
joints were cast including grouting of
bearings top plinth. Once the wet joints
achieved the required strength, stressing
of longitudinal PT was commenced
followed by load transfer of Span to Piers.
The Cable Stay Bridges
It is for the first time that a cable stay
bridge has been attempted on open seas
in India. The aesthetically designed
pylons have an extremely complex
geometry and one of the longest
spans for concrete deck – presenting a
formidable engineering challenge. The complex pylon geometry was
another challenge for surveyors. HCC’s
Principal Surveyor devised a sophisticated
technology to measure coordinates
through a combination of total station
and prisms mounted on pylon legs.
The pylon legs were constructed within
an accuracy of ±5mm, which speaks
volumes about the technique employed.
Erection of Segments of Cable
Stay Bridge by Derrick
The balance cantilever method was used
for erection of segments at Cable-Stayed
Bridge. During construction, the length of
free cantilever for Bandra Cable-Stayed
Bridge was 215m and for Worli Cable Stayed Bridge it was 73m. The segments
were lifted by a Derrick which was fixed
on both ends of the pier table segment and
then forwarded. Lifting operation was done
simultaneously on both ends. At a time,
Derrick could lift one segment. Deck is
constructed of alternate stay and non stay
segments joined to pier table segments.
Dry Matching, Epoxy and
Temporary Stressing for Gluing
When the segment was positioned, it was
to be joined with the existing segment.
Therefore, the segment was first drymatched
with the already erected segment.
On completion of dry-matching, the
segment was moved back by sliding the
lifting beam for a distance of 400mm of
the derrick and epoxy was applied on the
face of both segments. After application
of the glue, the segments were joined
together and were stressed by Temporary
PT bars. Post this step, the segment lifting
beam on derrick was moved forward to
lift the next segment i.e. stay segment.
Erection of Stay Segment
These segments were also erected similarly
as the non-stay segment and were also
joined in the similar way. After this,
guide pipes were installed over the ducts
left behind during segment casting.
Stay Cable
Stay Cables used are ‘Parallel Wire Stay
Cables’. Each cable consists of a group
of different number of steel wires. Each
wire is made up of high tensile steel.
Diameter of single wire was 7mm with a
breaking limit of 6.28 Tones. Six different
sizes of cables were used in the cablestayed
portion. The difference between
them was only on the basis of number of
steel wires in each cable. Six different
types used were of 61, 73, 85, 91, 109
and 121 steel wires. Group of these
wires was packed in two layers of HDPE
(High Density Poly Ethylene) material to
protect them from atmospheric effects.
Closure Pour
In Bandra Cable-Stayed Bridge,
closure pour is provided between main |